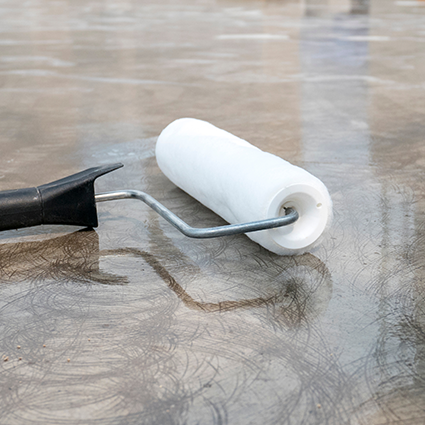
Epoxy Coatings Properties and Market Needs
Epoxy coatings are expected to have the following properties: resistance to a wide variety of chemicals, outstanding corrosion resistance, and adhesion to a wide variety of substrates including marginally prepared metal surfaces and concrete.
When developing new additive for the epoxy coatings market, it is important to keep in mind that any added ingredient can enhance performance in one area while detracting from performance in another. Also, current high performing products can be quite complex and adding a further new ingredient increases the complexity even more. A good additive will address or target multiple aspects of an epoxy coating and strive to improve or replace two or three properties simultaneously in order to add value to the new raw material and reduce the complexity of existing formulations.
Currently there are separate raw materials used to enhance adhesion to various substrates, improve corrosion resistance, aid in improving impact and bend properties, as well as improving gloss for aesthetic purposes. These ingredients often do not complement each other. For instance, adding low molecular weight low viscosity mono functional epoxies can increase flexibility but reduce adhesion. Still other additives are used to lengthen pot life and shorten cure time, especially in cold weather, but this comes at the cost of color and toxicity. A current trend in the industry is to reduce VOC levels without impacting any other properties of a coating. In addition to this, the market is requiring thinner coats while maintaining performance.
Reducing VOCs in epoxy coatings is particularly challenging since the reduction of solvents generally leads to significant viscosity increases. This increase causes difficulty in mixing and application of these two component systems. In order to counteract this problem, lower viscosity, lower molecular weight resins are employed. These require more hardener to build molecular weight and cure, and the additional crosslinking in turn embrittles the final epoxy coatings reducing impact resistance and flexibility among other properties. These epoxies also contain higher levels of functional groups requiring more of the costly hardener to cure. This not only increases costs but also increases the latent heat of the system greatly reducing the workable pot life.
To this end, an ambitious project was undertaken to develop a single multifunctional additive, allowing the removal of existing additives and enhancing the final product performance. The base formulation was to be a simple, low VOC system, consisting of a liquid epoxy resin and an adducted cycloaliphatic diamine. The following objectives were targeted:
- Develop chemistries to improve barrier properties to chloride ion migration, the key contributor to corrosion in harsh environments.
- Impart attributes that provide flexibility and impact resistance to a system that has neither of these.
- Provide attributes to maintain or improve adhesion
- Invent functionality that will improve pot life and cure time
- The additive must also enhance aesthetics such as gloss or color.
- No added VOC’s
– Gerald Vandezande